2024 - 2025 Season

2023 - 2024 Season
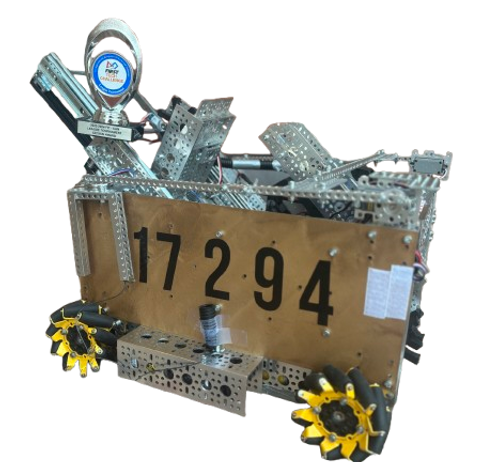
2022 - 2023 Season

Build

Drivetrain

Lift
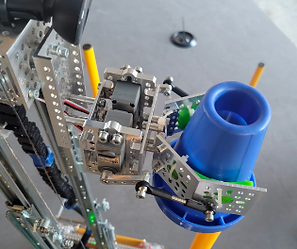
Claw

CAD Model
Our build team works on assembling goBilda parts and motors with the REV hardware parts to create the robot
2021 - 2022 Season

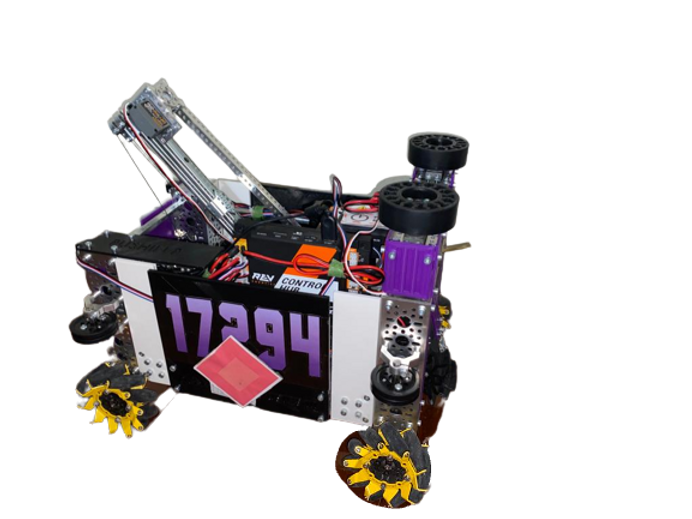
Build
Our build team works on assembling goBilda parts and motors with the REV hardware parts to create the robot

Drivetrain
We created a thin design with clearance to let our robot easily go around or over the barrier, while using miter gears to transfer motor motion to the wheels
Carousel Spinner
2 carousel spinners tuned to the best possible speed use servos to turn the carousel.
Robot Intake
Using a gecko wheel, vertical motor, and a surgical string, our intake is able to take in various items into our bucket
Bucket and Lift
The bucket carries the item while the lift uses viper slides and a motor to quickly ascent the item upwards.
Capping System
A servo with is able to quickly attach to the team shipping element using a magnet and detach it with a twist from the robot




CAD Full Cad Link
Computer Aided Design is a helpful tool for our team to design various components of our robot. Before designing various mechanisms, we download parts from sites such as GoBilda and create assemblies. Additionally, we also design some custom parts for our robot, some of which can be seen below.

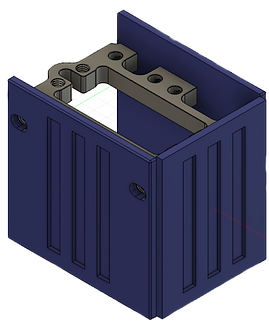
Carousel Servo Shield

Capstone Rod Magnet Holder

Front Shield

Intake Motor Shield
Special thanks to SainSmart!
SainSmart was able to provide us with 9 rolls of filament! This helped us 3D print the parts that covered our robot, adding structure, durability, and aesthetic to our robot!

Programming

.png)
We use Java to program our robot, using Android Studio and GitHub. We also use Roadrunner which is a Java motion planning library written for the FTC competition. We also code autonomous paths for our robot which work before the driver-controlled period.
There is also a lot of strategy used when programming, such as what controls to add for our robot and how our autonomous periods should be pathed.